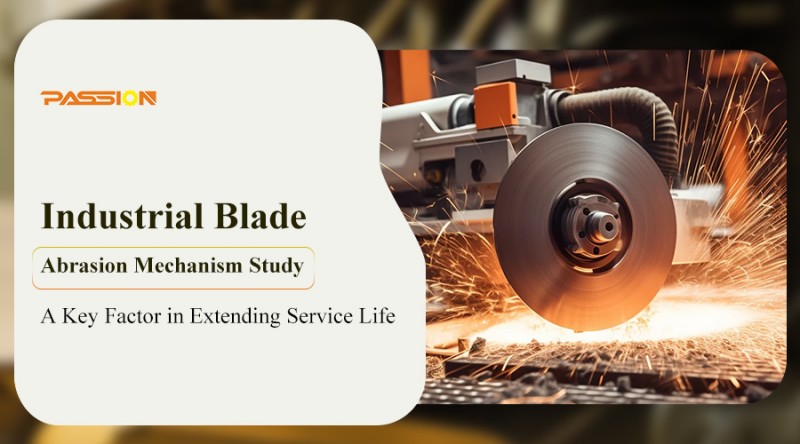
Tööstusliku tootmise valdkonnas on tera hõõrumine alati olnud oluline tegur, mis mõjutab tootlikkust ja toote kvaliteeti. Teaduse ja tehnoloogia edenemisega ning protsessi pideva optimeerimisegatööstuslik teraHõõrumismehhanism on muutumas üha põhjalikumaks, eesmärgiga leida peamised tegurid tera kasutusaja pikendamiseks.

Tera hõõrumisel on mitmesuguseid põhjuseid, sealhulgas peamiselt mehaaniline kulumine, termilise kulumine, keemilise kulumise ja difusiooni kulumine. Mehaanilise hõõrdumise põhjustavad peamiselt tooriku materjali kõvad osakesed, et teha tera pinnal soonte, ja selline hõõrdumine on eriti ilmne, kui vähendatakse madala kiirusega. Termiline hõõrdumine on tingitud lõikeprotsessi käigus tekkivast suurest soojusest, mille tulemuseks on tera hõõrdumise või termiliste pragude plastiline deformatsioon. Keemiline kulumine on õhus hapnik kõrgel temperatuuril ja tera materjali keemiline reaktsioon, madala kõvadusega ühendite moodustumine, kiip eemale, põhjustades tera hõõrdumise. Teisest küljest on difusiooni hõõrumine see, et lõikeprotsessi ajal difundeerub tahkis koosseisus ja tera hõõrdumise keemilised elemendid tahkis, muutes tera kompositsioonistruktuuri ja muutes selle pinnakihi habraks.
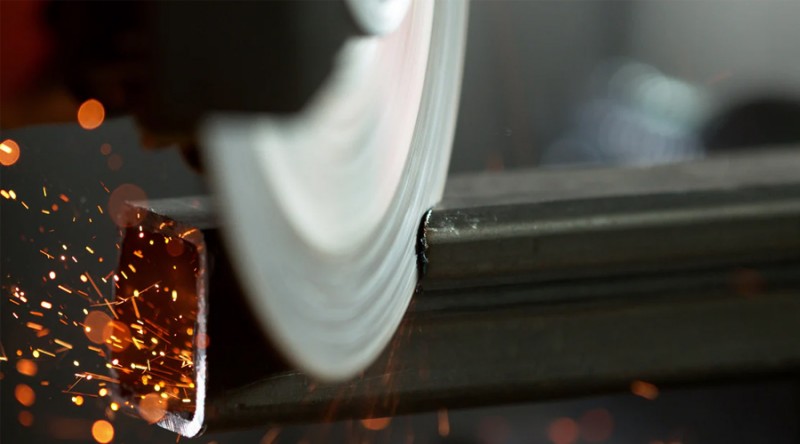
Nende kulumismehhanismide jaoks on teadlased pakkunud välja mitmesuguseid meetodeid, et pikendada tera hõõrdumise kasutusaega. Esiteks on võti mõistlik valik teramaterjalid. Vastavalt töödeldud materjali ja lõiketingimuste omadustele, võib piisava karedusega terade, kulumiskindluse ja sitkuse valimine tõhusalt vähendada hõõrdumist. Näiteks kui töötleda raskesti lõigatavaid materjale, millel on suur kalduvus kõveneda, tuleks valida tugeva vastupidavusega külma keevitamise ja tugeva difusiooni vastupidavus.
Teiseks on terade geomeetria parameetrite optimeerimine ka oluline vahend kasutusaja pikendamiseks. Mõistlik tera nurk ja tera kuju võivad vähendada lõikejõudu ja lõikamist ning vähendada tera hõõrdumist. Näiteks esi- ja taganurkade sobiv vähendamine ning suurema negatiivse serva kalde kasutamine võib vähendada lõike serva kulumist. Samal ajal võib negatiivse faakri või servakaare lihvimine parandada ka tera otsa tugevust ja vältida hakkimist.
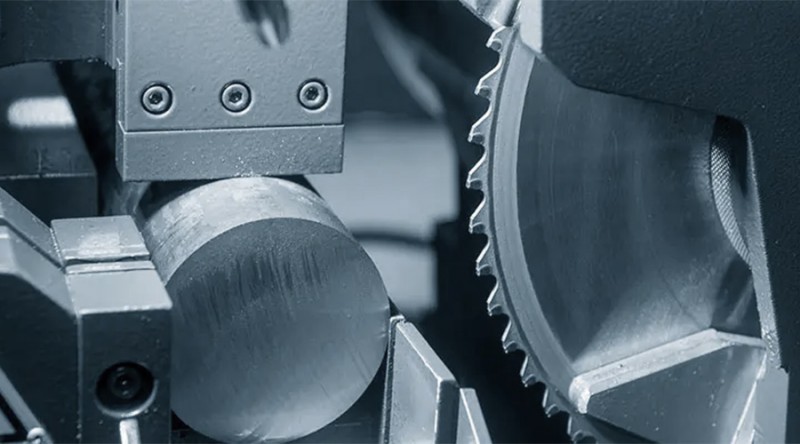
Lisaks on tõhus viis terade eluea pikendamiseks ka mõistlik valik lõikeannuste ja jahutusmäärde kasutamine. Lõike ja sööda sügavus on liiga suur, lõikejõud suureneb ja tera hõõrumine kiireneb. Seetõttu tuleks töötlemise tõhususe tagamise eeldusel vähendada lõikekomu. Samal ajal võib jahutusmäärde jahutusmäärde kasutamine imada ja ära võtta suurema osa kuumusest lõiketsoonis, parandada soojuse hajumistingimusi, vähendada tera ja tooriku lõiketemperatuuri, vähendades sellega tera hõõrdumist.
Lõpuks on tegurid, mida ei saa ignoreerida ka õige töömeetod ja protsessisüsteemi jäikus. Lõikamisprotsessis peaks tera proovima panna tera ei kanna või vähem koormuse muutumist ei kanna, et vältida ebaühtlast jõu ja purunemise tõttu tera. Samal ajal, tagamaks, et protsessisüsteemil on hea jäikus, vähendada vibratsiooni, võib samuti tõhusalt pikendada tera kasutusaega.
Kokkuvõtlikult hõlmavad tööstuslike insertide kasutusaja pikendamise peamised tegurid mõistlikku terade materjalide valikut, tera geomeetria parameetrite optimeerimist, mõistlikku valiku annuse valikut, jahutusõpikute kasutamist ja õigeid töömeetodeid ja protsessisüsteemi jäikus. Terade hõõrdamise mehhanismi pideva süvenemisega arvatakse, et tulevikus ilmuvad uuenduslikumad tehnoloogiad ja meetodid, süstides uut elujõudu tööstusliku tootmisvaldkonna arengusse.
Hiljem jätkame teabe värskendamist ja lisateavet leiate meie veebisaidilt (PassionTool.com) ajaveebist.
Muidugi võite pöörata tähelepanu ka meie ametlikule sotsiaalmeediale:
Postiaeg: 15. november-20124